It’s been said that the definition of insanity is trying the same thing repeatedly while expecting different results. Similarly, when it comes to product drawings, you can only adjust a new design so many times before recognizing that it’s time to move on to the next step and seek advice on how to optimize it for production.
In the microfluidics world, complex shapes and stack-ups are able to facilitate chemical analysis of small volumes of fluids, which has reduced hospital visits and overall healthcare expenditures. However, this sophisticated technology requires very precise instruments. As a result, the demand for microfluidic prototyping is rising rapidly because it can be a great tool to avoid getting stuck in the drawing creation phase.
At Strouse, we’ve spent over thirty-eight years building custom product components, including a diverse range of microfluidic products intended for diagnostic applications.
In this blog post, you’ll learn how to plan your microfluidic diagnostic designs to ensure a smooth and cost-efficient manufacturing process.
Key Factors To Consider in the Microfluidic Device Design Phase
Whether this is your first or fiftieth microfluidic application, this article will offer advice on creating microfluidic devices through rapid prototyping and improving them until they function as best as they can.
1. RELIABILITY AND CONSISTENCY
Microfluidic devices have powerful diagnostic abilities, for example, they can be used as test kits for early detection of infectious diseases.
You’ve likely heard about some COVID-19 tests resulting in “false negatives” and how these results impact the lives of patients, their families, and the community. Some of the false negatives were caused by microfluidics devices that weren’t fully prototyped. Now more than ever, having reliable diagnostics tools will help:
- Control the spread of infectious diseases
- Provide timely treatment
- Better manage patients
Of course, the usefulness of microfluidic cartridges extends far beyond diagnosing the coronavirus. Many point-of-care (PoC) applications diagnose more common health issues, from blood sugar and blood pressure tests to diabetic strips. They all rely on the speed, ease of use, low cost, and reliability of microfluidic devices.
So, how can you guarantee that your part components have precise microfluidic channels and other essential elements that contribute to flow rates and diagnostic accuracy?
Manufacturers often use precision die cutting to achieve reliable, high-volume, consistent tolerances and ensure proper part function. In fact, die cutting (sometimes used in tandem with laser cutting) is the production method that Strouse uses most commonly when building custom microfluidic parts.
2. SCALING (A.K.A., THE CHALLENGE OF CREATING MILLIONS OF MICROFLUIDIC DEVICES)
You can spend an hour etching a design into a piece of plastic, but if it’s not replicable, is it really a reliable business model? A lab-on-chip (LoC) is made of molded plastics or laminates and is usually produced in large quantities, which makes diagnostic testing low-cost and high throughput. Within it, the fluid must flow in a specific way and precisely combine with different materials to get accurate results.
When you’re early in developing your LoC microfluidic cartridge, you may perform the assembly by hand. However, when volume increases, the only way to accurately apply layer upon layer of material in quantities in the millions is to use automation Designed For Manufacturability (DFM). A converter must develop the right manufacturing process to meet specific functional requirements in huge quantities.
Moving fluids within a microfluidic device requires using specific surface energy materials for microfluidics with certain material thicknesses and cutting highly precise width channels, which requires high tolerances. Any variation means the fluid doesn’t flow at the correct speed or doesn’t flow at all.
The “micro” part of microfluidics means a device may have features requiring laser cutting instead of traditional hard tooling. For instance, imagine a part with 14 layers, each with its own complex shape, that must be cut precisely and then placed upon another 6-layer stack with every layer requiring a tight tolerance die cut, some within one-half of a millimeter. Only automation (a robot with a camera eye) can pull off this level of precision, but ultimately it will be dependent on the specific design and materials you choose.
3. MATERIALS AND DEVICE CONSTRUCTION
With design for manufacturability in mind, and knowing that millions of microfluidic devices will need to be manufactured, what are the biggest challenges in developing practical PoC diagnostic tools?
The first might be selecting materials to construct a device that meet parameters such as size and weight. From a converter’s perspective, a microfluidic chip can be seen as a complex, channeled, multi-stacked, flexible material on a roll that can be automatically dispensed and packaged. In order to succeed, tight tolerance die cut components need to be scalable, and your material choice will affect this to some degree.
On a related note, a device’s reagent media is often part of the construction process, requiring certain environmental factors to exist during manufacturing: keeping a steady temperature and humidity level as well as minimizing light that may cause the reagent to degrade.
A fully controlled environment—a cleanroom with controlled temperature/humidity and monitored air particles—is mandatory when creating *nearly* any medical device, including microfluidics. The cleanroom dramatically reduces the risk of biological contaminants (e.g., skin cells or hair) interfering with the function of diagnostic tests.
Lastly, in a microfluidic setup, adhesives must be selected specifically to be used near fluids, such as hydrophilic and hydrophobic adhesives.
4. SPEED OF DIAGNOSIS, TREATMENT, AND PRODUCTION
When you’re sick, you want a quick, accurate diagnosis and treatment as soon as possible. Microfluidic devices are increasingly becoming labs-on-chips, able to perform multiple tests on a single, amplified sample. They can even break up DNA chains to determine future health-related tendencies.
With such fast advancements, converters are challenged to design and build microfluidic devices for high-speed manufacturing. Of course, we must ensure each is reliable and consistent, so you’ll want to entrust your project to a company with reliable quality standards and quality control inspection processes.
Prototyping Your Microfluidic Design
There are many different ways to achieve a successful prototyping process; however, you should always choose the option that best suits your project goals.
For instance, samples are often created using prototyping methods that may not fully reflect the final product (such as making laser cut parts when the final design is die cut for quantity). If you need a sample that’s fully accurate to the final production method for validation & verification, then you’ll want to specify this when you contact your converter.
Whether you’re looking to create a single microfluidic layer or an entire stack-up, we can help you begin planning for an efficient manufacturing process.
If you’re searching for microfluidics laser cutting or are otherwise interested in flexible microfluidics production, Strouse has the experience and capabilities to help you build your design. Our rapid sample-making process will send you a part prototype based on your technical drawing as soon as possible.
Now that you know more about microfluidic design, feel free to reach out to us with any questions you may have. You can also find more information in our Learning Center.
Originally published: December 10, 2020
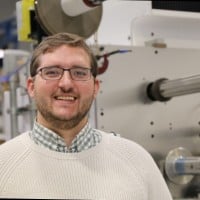