How does your adhesive converter prevent faulty parts from reaching you?
Quality inspections are necessary for every manufacturing process, but your needs may vary depending on the product.
At Strouse, all of the parts we produce go through some form of inspection, the extent of which depends on the job specifications. If you’re planning on ordering parts from a converter, familiarizing yourself with the quality control process might help you find a converter who can meet the necessary standards for your process.
Let’s discuss what goes into quality control inspection so you can make the best decisions for your product.
How Part Inspection Adds Value To Your Process
Simply put, defective parts will cost you time and money. Using a converter that takes the proper manufacturing precautions against part defects will protect you from product failures and a loss of consumer trust.
What Are Our Inspection Equipment Capabilities?
One of the first things we get asked about inspection as a converter is our equipment capabilities. Inspection equipment helps a converter monitor product for defects.
When thousandths of an inch can determine a good part vs. a bad part, it’s crucial to use precise equipment and rigorous inspection processes that suit the customer’s needs. However, not all products require the same level of inspection, so you'll want to account for the level of precision you need.
DIMENSIONAL INSPECTION
Dimensional inspection involves evaluation of the dimensional characteristics of a product and comparing them against the dimensional requirements– specification and tolerance limits- for that characteristic.
The choice of metrology tools for dimensional inspections depends on the specific part, the characteristic being measured, and the required level of accuracy.
HAND TOOLS
For straightforward measurements, hand tools like calipers, micrometers, and steel rules are commonly used. Micrometers and calipers are ideal for measuring material thickness or stack-ups, while calipers are also effective for determining the width and diameter of roll goods. For basic dimensions with assigned tolerances that do not demand extremely high accuracy, a simple steel rule is sufficient.
VIDEO MEASURING SYSTEMS
Video measuring systems, such as coordinate-measuring machines (CMM) and Quick Measurement Systems, allow converters to verify part dimensions.
Coordinate Measuring Machines allow for manual or automated measuring of samples. The field of view can be digitally overlaid with crosshairs or other features, and the stage or camera can be moved through manual controls for quick one-off measurements. Alternatively, the system can be set up with a programmed automated routine to collect the data.
Quick or Instant Video Measuring systems take a picture and reference that photo to determine the desired measurement data. This method is especially helpful for parts with many features.
FUNCTIONAL and PHYSICAL PROPERTY TESTING
To assure products meet functional or performance requirements, Strouse uses equipment such as a peel-tester and probe-tack tester to measure pressure-sensitive adhesive characteristics. Additional test methods (e.g., a T-test to discern respective sides of a differential liner) may be utilized to evaluate other material or product characteristics.
How To Determine Sample Sizes
If a sampling plan is not otherwise prescribed, we typically perform our sampling based on our unit size (each roll, box, etc.) to match sampling intervals with natural breaks in production to limit disruption to the process. With this, we also typically aim for sampling to occur once or twice an hour to provide adequate monitoring of the process and feedback to the operator.
SAMPLING CRITERIA
For certain projects or customers, standard sampling procedures such as ANSI, Z1.4, ANSI Z1.9, or Squeglia C=0 may be employed. These plans provide a recognized standard procedure for determining sample sizes and acceptance criteria based on lot size, inspection level, and a chosen Acceptable Quality Limit (AQL).
The Acceptable Quality Limit (AQL) determines the acceptable number of rejected parts before the lot is considered unfit. The lower the designated AQL the tighter the requirements. With the Squeglia C=0, A.K.A. the “zero defect” or “zero acceptance,” fewer samples are typically required, but a single defect will result in the rejection of the entire lot.
Pre-Production Reporting
At the onset of a project a pre-production activity may be requested to validate or verify a manufacturing process is capable of manufacturing product to the design specifications. Three typical pre-production activities and reports we see are FAIR (First Article Inspection Report, PPAP (Production Part Approval Process), and Process Validations.
The FAIR (First Article Inspection Report) comes from the aerospace industry and focuses on product construction, including the materials used and the evaluation of the part to confirm compliance with the product specifications.
PPAP (Production Part Approval Process) comes from the automotive industry, but different industries have co-opted one or the other. The PPAP provides for a comprehensive review of the production process, including supporting documentation such as process flow, control plan, measurement system analysis, and Failure Mode and Effects Analysis (FMEA), as well as evaluation of the parts themselves, which includes collection and analysis of measurement data.
In our application, Process Validation typically follows the Installation Qualification (IQ), Operational Qualification (OQ), and Performance Qualification (PQ) methods. Process Validation ensures that equipment and processes meet the project requirements.
IQ verifies that the equipment is installed correctly and operates as intended within its designated environment. OQ ensures that the equipment functions as intended and produces conforming product under various operational conditions, including worst-case scenarios. PQ confirms that the process consistently and repeatably produces conforming product in routine production.
Quality Control Inspections in Production
At Strouse, we ensure that there are about four points of inspection before, during, and after production.
1. SET-UP INSPECTION
Before the product runs on the press, Strouse double-checks the measurements, construction, function, quantity, documentation, material, and more. Once we’ve verified it all, it’s time to run the order.
2. IN-PROCESS INSPECTION
In addition to monitoring the process operation and parameters, Machine operators inspect product per the prescribed in-process sampling plan during manufacturing to ensure conformance to product specifications is maintained throughout the run.
3. FINAL PRODUCTION INSPECTION
At the end of the run, a Quality Assurance associate will inspect part samples as a redundant check to ensure they meet dimensional specifications, have the proper construction, and function as expected. This includes confirming the stack up of materials is correct, adhesive is laminated to the correct side of the liner, perforations or other functional features behave as expected, waste material is removed (matrix and slugs), and part dimensions are correct including placement and size of internal features.
Then, documentation is checked to confirm quantities produced, that the run record was filled out as required, and that all requirements were considered and met.
4. PACKAGING AND LABELING
The final acceptance and release stage takes one last look at the packaging, labeling, and shipping documents to ensure correct information, spelling, format, and that all documents are prepared and included.
Each project has its own quality control requirements, so if you’re in any doubt about whether a converter can match your needs, you’ll want to ask about it directly. Because everything we do is custom, our quality controls for each project are also custom-tailored to meet our customers’ needs.
Don’t settle for countless quality mistakes when you could be saving far more on a more accurate, more efficient process. Reach out for a flexible material consultation and consider switching to a more efficient converter today.
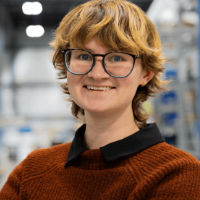