Are you researching which materials fit your product design?
If you’ve already combed through the sea of ancient engineering forums, you’ll know that there’s only so much you can glean from ten-year-old online threads posted by GasketLover777. Finding a suitable material relies on more than a couple of questions; realistically, there can be hundreds of factors to consider.
Strouse has spent over thirty years accumulating hands-on experience with a wide array of flexible materials. This guide is the direct result of interviewing product engineers about the most crucial aspects of material choice.
Regardless of where you are in your product development process, we can provide tips to help lead you in the right direction.
This guide won’t decide the exact product number of material you need to purchase, but it will give you a better idea of how you can create a cost-effective solution. If you’re developing a design, the following guide will help you learn how to find the best material for your needs.
How To Select the Right Product Material
In an age where everyone is accustomed to doing their own research, you likely already have a product material in mind. Still, you might be stuck between multiple variations, thicknesses, or suppliers. These design and development process tips will help narrow your options to find the right product.
1. ASK, “WHAT IS IT DOING?”
The ultimate reason to choose a product material is because it contributes to your part’s functionality. Whether your part is sealing, damping, carrying heat, or more, each function points towards certain materials. If you want to achieve the best product, you’ll choose a material that lends itself to your design’s purpose.
2. PLAN FOR THE ENVIRONMENTAL CONDITIONS
The first question to answer is whether the application is inside or outside. Some materials behave differently based on the temperature or humidity of the environment. For example, certain adhesives will not stick when applied in subzero temperatures.
Other materials may experience shrinkage or growth due to humidity, temperature, or other factors, which can affect their tolerances and cause issues in different areas, such as automatic placement or performance.
Make sure you’ve considered each aspect of the product’s environment to ensure a successful application and function.
3. USE ONLY YOUR NECESSARY TOLERANCES
When submitting a design for manufacturing, you should only use the necessary tolerances to find a suitable material.
Many product drawings possess title block tolerances, which are often far more precise than necessary. Tight tolerances are far more challenging and expensive to manufacture, so it’s in your best interest to confirm whether your tolerances are accurate to your application’s needs.
It’s far more challenging to achieve tight tolerances when cutting certain materials, such as thick foam and rubber. Using functional tolerances in your design will help ensure that you select a material that can hold your tolerances along with a matching process.
4. INVOLVE YOUR CONVERTER & OTHER MANUFACTURING PARTNERS
You’re probably thinking, “But wait! YOU guys are converters.” Yes, it’s true. But we’re not trying to pull the wool over your eyes—we’ve seen issues caused by material choices that aren’t intended for optimized manufacturing.
As a converter, we can help clients successfully navigate the material selection process by taking their production goals into consideration.
Material selection is vital to your product’s functionality. It can also affect the type of machinery or tools used in production or your design measurements.
You might not realize how much the material selection process affects the manufacturability of your design, but choosing a suitable material will set you up for both production and financial success.
Being a converter gives us multiple advantages for material selection:
- Our existing relationships with suppliers allow for better material pricing.
- We can obtain sample rolls of material for testing or building prototypes.
- We have the experience with flexible materials to navigate common pitfalls
In addition, we can compare suppliers' similar products to see which are more cost-effective or manufacturer-friendly.
5. CONSIDER THE FORMATTING OPTIONS
Certain materials only come in a specific format, which could be an issue depending on the type of process you’re planning to use. Rotary die cutting (used to produce large quantities of products rapidly) uses rolls of material rather than sheets.
Additionally, purchasing longer material rolls (better for converting) helps you save because they don’t have to be exchanged as often on a machine press, leading to less downtime for roll changes.
Let’s say that your material comes on a roll, but the roll is only 5 yards long: our press goes down every 5 yards; plus, if you only need, say, 10,000 rolls, the machine will only be running <10% of the time.
If you’re open to alternative materials or formats, you’ll find it easier to find cost-effective options for your product.
6. BE AWARE OF YOUR DESIGN FLEXIBILITY—OR LACK THEREOF
You might contact a material supplier initially who will match your needs on a base level. However, the first product you get might not be the most cost-effective or the easiest to convert. If that material gets locked in, you might be stuck in a bad situation.
Even if you have a material in mind or samples for a material that you’ve already specced in, our engineers will likely ask whether you’re open to alternatives and check to see if there are better options. Having these conversations early in product development helps get things in place before your design is locked and possibly submitted for FDA approval.
So, what happens if your chosen material is non-changeable?
If you’re working with Strouse, we’ll do the best we can with our resources. Sometimes, there simply aren’t alternatives, and this can lead to creative solutions on our end. Regardless of the situation, communicating your design and material fluidity is in your best interest.
Commonly Missed Considerations
- Have you considered alternatives? Another material might cost less or function better in manufacturing.
-
- Are there reasons you aren't using other materials? (if so, tell your converter!)
-
- Are you using low-surface energy (LSE) materials?
-
- LSE materials like nylon are far more expensive.
-
- Do you need to be worried about material or adhesive outgassing?
-
- Certain materials will outgas in heat or other conditions and erode the adhesive.
-
Testing Your Material Selection For Product Design
You can read hundreds of material datasheets, but testing your material will allow you to gauge its performance in your finished product.
Many suppliers offer test rolls, which may help you better understand whether the material matches your requirements. Yet, you won’t know if the material is going to perform as intended unless you test it in its desired shape. Having an accurate prototype allows you to test the capabilities of your design.
Getting a sample of your product will allow you to test it for its intended application and confirm your material selection based on its performance.
Finding material is no easy feat, but collaborating with an experienced converter will help you find and test functional, cost-effective solutions. Request a material sample or contact us if you want to develop a functional product.
For more guidance on product design, see the first part of this series or the content in our Learning Center.
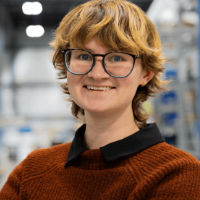