Developing a medical device is neither simple nor straightforward, so when you need dependable components, partnering with a trusted supplier may be the best option.
Strouse has helped develop hundreds of medical device components. We understand that every company has its own needs, so we tailor our advice and solutions to our customer-specific requirements.
If you’re looking for medical device solutions, you’ll want to learn more about outsourcing before deciding whether it’s right for you.
What Does Outsourcing Solutions For Medical Devices Mean?
Medical devices are typically composed of many different product components, from screens to skin adhesives to flexible circuits.
It isn’t always practical for a single company to specialize in each type of solution, so medical device manufacturers often outsource custom components from contract manufacturers to save money in their assembly process.
What Are the Advantages of Medical Device Outsourcing?
If you’ve looked into purchasing components, you’ll recognize that outsourcing has multiple benefits.
1. NO UPFRONT MACHINE COSTS
Equipment can be a major expense for any new project, but by outsourcing component production, you avoid the need to invest in specialized machinery for specific tasks in your process.
Complex die cut machines can range from hundreds of thousands to millions of dollars, depending on your project needs. This doesn’t even include the ongoing maintenance costs or the storage space required for equipment, tools, and materials.
In addition, die cut machines often require experienced operators to handle, which adds to labor, training, and trial-and-error expenses. Meanwhile, a converter already has trained operators and equipment to build your product solution.
2. PRODUCT DEVELOPMENT ASSISTANCE & EXPERTISE
While your company has its area of expertise, transitioning from product development to full-scale production is complex and requires skill to navigate cost-effectively.
Building a custom design isn’t as simple as feeding the drawing into a computer and clicking your heels together three times. Instead, designs often require adjustments before they’re fit to run on a machine press.
Converters can enhance your medical device manufacturing by recommending cost-saving improvements. They do this by streamlining your design: combining layers, offering alternative materials, and loosening any overly tight die-cut tolerances that aren’t essential.
Working with an expert will reduce your chances of encountering unforeseen issues or building an inefficient project process.
3. RAPID PROTOTYPING CAPABILITIES
Outsourcing manufacturing to certain companies allows you to use their rapid prototyping capabilities. Functional product samples will enable you to perform tests to ensure that the material and design perform as intended.
As a flexible material converter, Strouse uses our digital knife and laser to produce rapid prototypes. For larger testing quantities or validation and verification, we also perform die cut trial runs to ensure the construction of the final product to scale.
4. RELIABLE QUALITY STANDARDS
If you’ve manufactured products in the medical industry, you already recognize the importance of using proper manufacturing conditions and a precise quality control inspection process.
When you align yourself with a contract manufacturer, you can easily dictate your required quality standards without purchasing outside equipment or undergoing additional training. Check to ensure your partner meets the certification requirements for your needs, and you’ll have one less factor to worry about as you continue your product development journey.
Designing and building a medical device isn’t an overnight process but a formidable, multi-step endeavor. With all the planning involved, it can be a weight off your shoulders to be able to enlist experts for specialized components, like those in flexible materials.
Working with an experienced adhesive converter will help avoid delays and setbacks. With our highly skilled staff and proven die cut methods, Strouse produces precise, customized components for medical devices so you can launch your product on time and worry-free.
As a custom converter, our quoting process will examine your design and application process so we can start building a customized solution for your unique design requirements. To get started, contact us for a quote above.
Lastly, look at some of the additional resources in our Learning Center to learn more about medical device solutions and how converters optimize the manufacturing process.
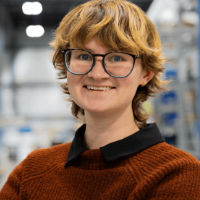