You’re sitting at your desk, staring at different prototyping services. A tiny voice in your head is crying, “But how do I know which one is better to use?!”
When building a custom design, it can be challenging to recognize the best approach for each step of the process. However, you won’t know how to proceed without an accurate prototype.
At Strouse, we choose the prototyping method based on the specific needs of each project.
If you’re stuck between digital knife cutting and laser cutting prototyping, don’t worry. Today, we’ll teach you the key differences so you can find precise samples that fit the scope of your project.
What is Laser Cut Prototyping?
Converters use laser cut prototyping to build rapid part mock-ups for material and design development. Although lasers can be used in full-scale production, prototyping refers to smaller sample runs of a handful to a few hundred parts.
Strouse uses a CO2 laser to create samples without purchasing a die cut tool.
Characteristics of laser prototyping:
- Capable of creating pressure-sensitive and registered cuts (allows you to make more complex designs, including tabs, multilevel parts, and other unique features)
- Capable of holding tight tolerances on most materials.
- Fastest and easiest prototyping method.
- May result in crispy, burnt, or otherwise charred edges depending on the material
- Not a good fit for thick and/or dense materials
- You cannot cut foils on a CO2 laser
What is Digital Knife Prototyping?
Digital knife prototyping uses an oscillating blade to cut programmed patterns and create varied designs. Like laser cutting, this prototyping method does not require the purchase of hard tooling and is, therefore, ideal for testing out designs.
Characteristics of digital knife prototyping:
- Very difficult to make registered cuts OR cut pressure-sensitive
- Material under an inch of thickness
- Foil is OK 👍
- Generally cleaner cuts, free of soot and debris.
- Generally slower and more labor-intensive.
- Edge condition of the cuts can be rough or coined, especially when cutting foils.
Laser Cut vs. Digital Knife Samples
Digital knife and laser cutting are good tools when it comes to sample production, but they do differ in multiple aspects.
1. QUALITY OF EDGES
Depending on the material, laser cuts can produce poor-quality edges with charring and debris, or melt it, causing the material to fuse to the liner. Digital knife cuts are free of char and soot, but depending on the material and process required to cut it, they may have rough or coined edges when compared to production tooling.
2. MATERIAL THICKNESS
Although you can laser cut thicker materials, they might require multiple passes of the laser, which could be inefficient for time.
For example, cutting a half-inch foam could result in crispy edges and multiple laser passes, whereas it’s a relatively simple cut to make through flash cutting.
Digital knife cutting is less sensitive to material thickness but limited by the material's durometer (hardness). Digitally cutting thicker polycarbonate will wear down and eventually break your blade over time. Ideally, you’d want to keep your materials under an inch of thickness for a digital knife.
3. ABILITY TO CUT FOIL
Unfortunately, metal's reflective properties make it unsuitable for a CO2 laser, so your converter may suggest prototyping with a digital knife.
4. SIZE AND SCALE OF DESIGN
Your part dimensions could affect the prototyping method depending on your converter's capabilities. For instance, the primary sampling laser we use at Strouse can handle designs within 2x3ft, while the digital knife can handle 5x5ft.
5. PROTOTYPING COST
Based on our experience, prototyping costs can vary greatly between laser and digital knife cutting. Cost is highly dependent upon the complexity of the design and the material(s) the part consists of. Typically laser cutting is the most cost-effective method to produce prototype samples, but your converter will need to weigh several variables before selecting one.
Building the Right Process For You
Building samples is one of the standard early stages of project development, but each company’s prototyping process varies depending on their current progress and budget.
If you want to explore laser cutting or digital knife prototyping, consider contacting us for a project consultation. Our engineers can help you prove out different designs using the method that best suits your project.
For more information on what we do and the processes we cover, feel free to check out our Learning Center for more details.
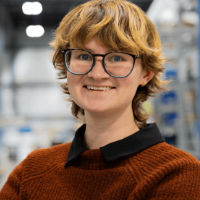