“Will I be able to peel this tape off?”
Like anybody else, you’ve probably struggled to remove tape at least once in your life. But when it comes to important projects, you don’t want to risk investing in rolls or part components that are challenging to peel off.
At Strouse, we take peel adhesion into consideration throughout the adhesive converting process to ensure product functionality.
If you’re looking to learn more about peel adhesion and how it might affect your projects, then buckle up as we explore.
So, What is Peel Adhesion?
Peel adhesion measures the force required to remove a pressure sensitive adhesive from a testing plate or its backing material. Testing a material’s peel adhesion will determine how challenging it is to remove.
Having the exact right peel-and-stick adhesion is vital during automated adhesive placement processes because the release liner carrying the adhesive must pull off just right, not falling apart when placed and not staying with the liner.
ADHESION VS COHESION
To fully understand the concept of peel adhesion, it’s crucial to understand two different yet similar terms: adhesion and cohesion.
- Adhesion refers to the strength of the adhesive or the sticky material to a substrate (the surface to which it sticks). It’s object-to-object interaction.
- Cohesion is the strength of the adhesive itself or the strength of its stickiness (not how well it sticks to a substrate).
For example, if you peel a piece of masking tape off a wall, leaving no residue behind, that measurement is its peel adhesion.
However, if you peel the masking tape and some adhesive stays on the wall while some stays on the tape, that’s a cohesive failure: you’ve exceeded the material’s strength, not so much the adhesion.
STANDARD PEEL ADHESION TESTS
Standard peel adhesion tests allow you to quantify the relative peel resistance of adhesive bonds in a repeatable manner, which benefits many areas of manufacturing.
One industry standardized test for these measurements is ASTM D1876: Standard Test Method for Peel Resistance of Adhesives (T-Peel Test). However, there are plenty of other tests as well as modified versions.
Thin materials often require tests to verify their peel adhesion for precise dispensing.
Permanent and Temporary Applications
Each adhesive solution is designed to perform in specific situations and environments. The application determines the amount of peel adhesion required.
In temporary applications — automotive paint masking, surface protection, wearable technology, removable labels — the goal goes beyond bonding two substrates; it’s also about how easily it’s removed and repositioned and how the surface looks after removal (see the part about residue below).
In permanent bonding applications, designed peel adhesion values ensure the bond holds based on the anticipated long-term forces. Meeting that limit — whether that’s in extreme conditions (a highway road sign, a construction site, a space shuttle) or stable conditions (medical devices, robotic systems) — combining the right components for the application is the key.
PEEL ADHESION AND BONDING SOLUTIONS
Any bonding solution’s effectiveness is always a combination of several factors: peel adhesion, substrate texture, chemistry, etc.
For example, a very high peel adhesion product may not be very good at sticking to a low-surface energy plastic. It doesn't matter how high that peel adhesion is; it just can't bond to that plastic properly.
To complement and complete a discussion on peel adhesion, ask your adhesive converter about shear: how a tape resists static forces applied in the same plane as the backing. Shear doesn't always relate directly to peel, but it’s related.
Is Residue Important?
Residue affects aesthetics AND functionality.
When you remove tape from a temporary application, the goal is to leave the surface as clean as possible. For instance, when applying a protective to an automobile part, it should lift up (peel off) without leaving any ghosting or adhesive behind.
In a medical application like pressure sensitive tape applied to skin, it’s essential for the adhesive to resist falling off while still causing little trauma to the skin when removed. Of course, in the case of slight residue left behind, it can simply be washed off.
If the goal of the application is simply to create a permanent or semi-permanent bond, the residue isn’t as important because these surfaces aren’t meant to be separated. Peel adhesion provides insight into the residue left behind once you remove the adhesive.
WHY IS RESIDUE LEFT BEHIND?
Factors that determine when residue is left:
• Type of adhesive used (and its strength)
• Cohesive strength (is it stronger than the adhesion?)
• The substrates you’re sticking to
• Application temperatures
How Does Peel Adhesion Fit into Your Project?
Working on a custom project? Peel adhesion is just the beginning. .
During a product’s design phase, converting engineers will use various testing methods to determine the right solution while the production team runs tests to validate that the product stays within the designed parameters.
If you’re struggling to maintain the right peel adhesion, consider reaching out to the experts at Strouse for a converting quote, which will start out with a project discussion as we start to plan potential solutions.
Originally published: March 24, 2021
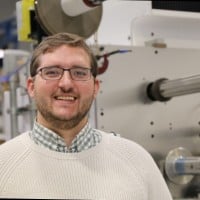