Automation isn’t the future. It’s here today, and without using it wisely, most companies are at a competitive disadvantage. Yet, automation isn’t an “all or nothing” decision. There are levels of automation, especially in converting, that make it easier to start working smarter and more efficiently.
This article explores various automation levels and uses examples to magnify the importance of automation within everyday converting projects.
The Customer, Not the Converter, Dictates the Automation Level
Once upon a time, manual manufacturing was the only way to assemble a product. Today, manual labor is far from extinct, but things have moved significantly in that direction. In the end, manufacturing has always been, and will forever continue to be, about meeting customer requirements and maximizing profitability.
When it comes to automation and technology, customers nearly always want to use the latest tools to increase productivity, if budget allows. Production goals can drive converters’ R&D efforts, which can include collaboration on what future equipment and engineering processes align with their goals. The way the goal can be completed most profitably is the winner.
The term “automation” can mean one thing to a manufacturer — maybe a single dispenser machine — while to another, automation is 150 dispensers in a very complex line. In addition to defining what automation means, what level of automation is best for their needs is also debatable.
Applying product parts by hand, or manual manufacturing, can be partially combined with automated equipment to be more semi-automatic. This could involve people moving parts from one stage to another in an assembly line, for instance.
In fully automated (all robot) manufacturing, the only human interaction within production processes may be loading input rolls and removing finished product. The rest of the process, from performing all actions to moving parts from one space to another, is all done by machines. This complex line needs to be foolproof before beginning production; otherwise, the line will stop and render the technology useless.
It comes down to an important question: What are you looking for from automation? Do you need to make more products? Make them more accurately? Make them more efficiently (is reducing labor the goal)?
Your answers drive your design for automation, similar to “design for manufacturability.” Once you know your goal, design around that goal. Does your product fit machines that are already in place, or are machines being purchased specifically to make the product? An experienced converter helps guide customers to proper determinations and the best processes.
The 3 Keys to Determining Automation Level
Automation is often the answer to a production challenge, yet that solution can be executed on numerous levels. Depending on the customer’s needs, the three factors that drive an automation level include:
1. Volume — “How many do you need?” Scaling up to meet demand is no simple task. If a company has been manually assembling a product and needs to increase production significantly, confusion (and possibly fear) may be the initial reaction.
Automation could be the answer, yet how many units usually triggers the use of automation? 10,000? 1 million? Even that simple request can seem like a mystery, at least at first glance, because it really depends on the product. A task that a person can accomplish manually in 3 seconds should be looked at differently than a task that takes 30 minutes to complete. The level of gain may not justify the expense of automation in some instances.
A complete throughput/capacity/needs evaluation is required to determine what volume triggers the use of automation, either semi or full. So, in theory, making 1,000 labor-intensive parts could be a great candidate for automation.
2. Time — “When do these need to be finished?” The speed a product needs to be delivered can change everything. If it’s needed immediately, full automation is out the window because it usually takes at least 6 months to develop, build, and get a fully automated line up and running. In contrast, you can get a semi-automated line up relatively quickly.
Here’s an example. A company wants to bring a part to market by year’s end. The product schedule needs to include designing a prototyped part (if it doesn’t already exist) in order to develop the machine and have it ordered by a specific date to meet the launch.
Then you'll need to design machinery and make 200,000 parts within the last 8 months of the year. You’ll be hard-pressed to meet that deadline with a fully automated line. However, you could get a semi-automated line up relatively quickly and start producing parts.
3. Cost — “What’s your budget?” A company may need to scale up to be competitive, yet the amount of available labor either can't get it done or can get it done, just too expensively. Automation is a likely solution, yet having a realistic budget is imperative.
As mentioned earlier, some manufacturers may already have the automation; a shiny, new machine. So, they want to engineer the part or product around its abilities instead of designing the part or product for automation, figuring out the best way to make it accurately and efficiently. Sometimes this can work, but other times, it may require a re-evaluation of the project.
Accuracy. Repeatability. Culture.
Humans can’t do everything. We can do a lot but not always accurately enough for some projects. Robotics are more accurate than the hand can place it, and sensors ensure precision in ways no person can. Plus, machines do it correctly time after time.
A good example is microfluidic devices. Imagine a 20-layer lab-on-a-chip device. Volume may only be 10,000 per month (a number that’s a candidate for manual manufacturing), yet the pieces require incredible precision to be assembled correctly. Automation is the ONLY way to go for products like these when a large amount of assembly is necessary, and repeatability is vital.
Here’s another, much different, example. A part needs to adhere to a simple plastic piece. Sounds easy, right? Well, it needs to be extremely accurate — even the smallest deviation causes the part to fail — so it can’t be done by hand. This process is a good candidate for semi-automated; a human does the setup, and the machine ensures that accuracy and repeatability are high.
Now, some converters aren’t able to consistently produce products that meet specifications. That’s when culture enters the picture, something that may not be top-of-mind when you consider automation, but you should.
Expensive automation — a piece of high-end equipment — is useless when the line shuts down because of poor quality. A true dedication to performance (accuracy and repeatability) sets some converters apart, so no matter what industry and what level of automation is required, the right converter can handle it.
Converter Guidance Makes it Happen
OK, now put all three keys to determining automation level —volume, time, cost — in a blender. Why? Because coordinating all of these, which is absolutely necessary, has to be done comprehensively, with the big picture in mind. This is why a converting partner dedicated to performance is so important.
One final example! A task, one of many in a long assembly line, requires a custom solution. A specific machine (a certain level of automation) may need to be built that performs that exact task. An experienced converter will work with an automation house to solve the problem. Then, it simply needs to be integrated into the assembly line.
To compete in manufacturing in the U.S., a company needs to apply some level of machinery automation. And as obvious as automation may be as an answer to a challenge, actually making it happen could seem like climbing a mountain.
Leaning on the experience and expertise of the right converter can take you far. Strouse, a 3M Preferred Converter, has delivered 5 billion discrete applications for automatic systems to Six Sigma quality at 1.33 Cpk (process capability index), or a 99.99% process yield.
Plus, Strouse’s automation equipment can make products for your automation equipment. What problems can automation solve for you? And how can Strouse help? Bring your thoughts or comments about automation to Strouse. Or, ask an engineer your questions today!
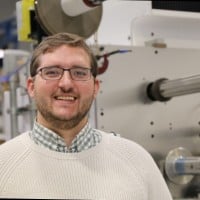