Microfluidic technology involves moving tiny amounts of liquids to perform various functions: ink in an inkjet printer, solder on an electronics board, bodily fluids within a medical device to perform chemical analyses. The use of this technology isn’t exactly new, but its popularity is rapidly rising.
Multilayered microfluidic devices — the majority of microfluidic devices — typically have channels built into the device through which the specific amount of fluid flows at a particular speed and path. Construction is accomplished by either adding channels between layers or subtracting material from a solid sheet to form channels. These individual layers eventually need to come together in one usable package or device.
Materials (most often flexible materials) used to build these valuable devices include films, foils, felt, nonwovens, and a variety of adhesives: optically clear adhesives, thermal adhesives, and heat-activated adhesives, among others.
We previously shared an easy-to-understand guide to microfluidic applications. Today, we’ll dig into what it takes to manufacture multilayer microfluidics devices.
How many layers? What do they do? How do they work?
A multilayer microfluidics device may have 2 to 20 layers, depending on its functionality. Here’s an example of one device’s format: one layer has a hole in it; the next layer has channels cut into it; the next layer has a hole in a different spot; the bottom layer is flat. That’s a very simple, 4-layer stack up.
A fluid sample (let’s say a drop of blood, for instance) is dropped into the top hole. Through capillary action, it’s drawn through the webbing channels, dropped through the other hole, and then tested. A consistent flow of the fluid is key; if tolerances aren’t met — and the channel is cut either too large or too small — the flow changes, which leads to catastrophic failure.
What may sound simple actually depends on extremely precise converting and assembling. Small, hard-to-cut features can be challenging in the wrong hands. Stacks can quickly become useless piles without tight tolerances and trusted repeatability.
A second way to use a multilayered stack is to drop fluid straight through multiple layers, with some layers containing reagents that the fluid absorbs, creating a mix. The added chemicals may cause the fluid to change color, signifying a completed test. Most COVID-19 tests and flu tests operate this way.
Care must be taken to keep layers free from any damage in either process, which could skew test results or prevent tests from being completed correctly. Some reagent materials are pretty brittle, making handling a challenge, so presses must run precisely to prevent damage.
Cleanroom ensures safety and reliability.
Multilayer microfluidics devices are complex products that require specific manufacturing processes. Impurities — dust, smoke, microorganisms, poor air quality, etc. — can promote the growth of bacteria and mold (causing defects), so most microfluidic devices need to be assembled in a cleanroom that has achieved ISO 7 certification, making it more than 100 times cleaner than an ordinary room.
Contaminants within unclean environments, or even the slightest DNA, can hurt a device's performance, creating false-positive or false-negative results. That can quickly lead to users perceiving that device negatively and ultimately losing market share.
Remember the reagents mentioned earlier? Many are sensitive to light and humidity before they are sealed within a device, so precautions need to be taken to achieve consistent, accurate, and reliable testing. Without proper care in the right environment, the reagents will fail.
The Importance of Converters
Some microfluidic devices are designed flawlessly and are ready for converting processes. More often, however, the converter provides guidance and offers advice on making the device designed for manufacturability (DFM), especially when huge quantities put extra pressure on the manufacturing process to be precisely correct.
Converters understand what shapes and sizes are possible and what tolerances are realistic for specific devices. Naturally, OEMs design devices that are as small — and tight — as possible. Typically, there are beneficial exchanges between the OEM and the converter when it comes to design.
Yes, a material's ability to be converted is important, yet just as vital is the assembly process aspect of converting. Even with convenient tabs on specific layers to make placement easier, manually assembling multiple layers by hand can reduce accuracy and quickly escalate costs. Converters help transition multilayer stacks from manual to automated assembly (more on this later).
From 14 to 9 Layers
What should a converter do when a customer shares 14 drawings for a 14-layer stack? An experienced converting partner will instantly begin scrutinizing the drawings, looking for opportunities to consolidate steps and reduce layers. Perhaps two or three layers can be built together; maybe that can happen a second time, too. With a little effort, the number of layers needed has been reduced down to 9, saving material and labor costs.
Reviewing what layers touch each other can make a huge difference. A reagent may need to be separated from another reagent by non-reactive layers, so reducing layers may not be possible. Again, it all depends on the function and design of the device.
“The sample is great. Now, make 20,000,000 of them.”
Many converters can produce a pristine sample; an exact part that nails the shape, size, thickness, layers, etc. However, the all-important aspect of converting is scaling up to produce millions of the exact same part. There’s no room for error when bringing ideas and concepts to market.
A converter like Strouse helps develop and integrate fully automated assembly processes, reduce human error, and make large-scale production possible when the demand is there. Having experience scaling up by using automation sets these highly sophisticated converters apart from others who may only take on simple converting jobs.
Relationships aren’t formed by simply following product drawings. Strouse takes pride in collaborating, sharing, discussing, and then solving problems. As OEMs demand more from devices and adhesive manufacturers push the limits of science, more than ever, it’s wise to partner with a full-service adhesive partner to bridge these two and offer highly effective solutions.
Learn more about flexible material converting by reading our guide: Flexible Material Converting Q&A. If you have specific questions about microfluidic technology, give Strouse a call at (800)-410-8273 or ask an engineer!
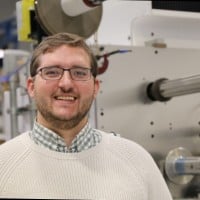