Q: “Hey, can you make me two gaskets?”
A: “...Have you tried the home-improvement store?”
Generally speaking, any quantity is feasible if you’re willing to pay its costs. However, visiting a flexible material converter might not make much sense depending on your long-term goals and project budget.
When you purchase a low volume of parts, the set-up and inspection costs take up a far more significant portion of your budget than the machine run time.
Strouse has accepted orders ranging from tens of parts to millions, so we’ve experienced and adapted to low quantity orders firsthand.
Now, let’s review the quantity standards for Strouse’s orders so that you know why low quantities are more challenging to produce and how it can affect your die cut order.
Is There a Minimum Quantity for my Die Cut Order?
Technically, there is no minimum quantity to order our parts.
Depending on your project size and chosen material, ordering certain part quantities might be a better long-term deal for you:
Strouse considers the following when suggesting order quantities:
1. Labor cost- Set-up time
- Inspection time
- Finishing
- Breaking down the press
- Minimum Order Quantity (MOQ)
Above all else, your order quantity has to cover your product needs. However, factors like labor cost or the cost of materials will help guide better deals and purchasing decisions that will benefit you over time.
LABOR COST
Your labor cost is the price of all set-up, inspection, or breakdown involved in the converting process.
Suppose you go, “Alright Strouse, I’d like to order one single die cut part.”
Although your converter COULD build you a single die cut part, it might cost something like $4,000.
When you order a low quantity, the labor cost is split up among fewer parts, creating an exorbitant unit price. Alternatively, making high quantity orders grants you a smaller price per part because the labor cost is spread out over a greater number of units.
Labor cost often comprises a large percentage of the total cost for low quantity orders. For instance, if the cost of one part was $4,000, a thousand parts might only cost $4,200 since the most considerable portion came from the machine set-up process.
Because of the labor cost of a rotary die cut press, converters often suggest alternative solutions for small orders like laser or digital cutting.
Setting up a rotary die press and making adjustments for a custom job can take hours, if not days to perfect. Laser and digital cutting is far easier and faster to set up, which helps to reduce your labor expenses.
If neither laser nor digital cutting works, and regular dies are too expensive, Strouse might consider flex tooling, a far cheaper albeit shorter-lasting version of die cut tools.
Ordering large quantities allows your converter to optimize your project set-up during the manufacturing process.
The more frequently Strouse runs your project through a rotary press, the more accurate the set-up process or adjustments become. The only way to get faster at assembling the press for your custom order is to practice.
Over time, we’ll become more efficient at setting up and building in-spec products without taking as much time or generating as much material waste.
MATERIAL COST
The Minimum Order Quantity (MOQ) is the most significant determiner of how much material you need to purchase for your order. The MOQ becomes an issue when it doesn’t align with the number of parts you’re hoping to order.
Even if you only wanted to build a single 5x5in piece, your desired material could have an MOQ ranging from 108 to 25,000 ft. A large MOQ poses an obvious problem to customers who understandably don’t want to buy excess material.
One way to potentially get around this is to get a sample roll from a material vendor, which are offered for very small quantities. This is one way to get through the prototyping stage, but once you move into validation, the MOQ becomes a bigger problem.
Remember that your material amount will also need to include any material used in the set-up process, so the actual amount of material could still be higher than anticipated.
Plus, because Strouse’s materials have an adhesive shelf life, we don’t usually stock material we aren’t using because they’re likely to expire.
If your converter has enough material, we can make as many parts as you order. Helping you decide your part quantity typically includes statements like this:
“We can make ____ parts out of the MOQ for this material.”
Balancing the MOQ with your desired number of parts is how Strouse creates cost-effective orders.
What Determines the Number of Die Cut Parts I Need to Order?
While there isn’t a specific number of parts to order to partner with Strouse, your order quantity will likely come down to what you need and are willing to spend.
If you’re using a trustworthy converter, they’ll be transparent about how the MOQ will affect your price and open to discussing whether your low part quantities are worth the inherent labor costs.
Are you looking for a small number of parts to start? Is there a strong possibility of wanting to scale up in the future?
Understanding the eventual goal of your part will help us determine how to build your process in a manner conducive to increasing production.
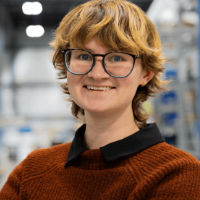