Your eyes burn as you stare at the computer screen, locked in a furious match with an email. The problem? Tooling costs.
To somebody who doesn’t know much about die cut converting, tooling costs may seem like they’re conjured from thin air.
Strouse has been around for over 36 years, which is long enough to witness exorbitant tooling prices, so we know how it feels to receive an unpleasant price tag. You deserve to know more about your tooling costs, so we’ve compiled the information to help you understand them.
By learning how and why Strouse covers part of your tooling costs, you’ll be able to make informed decisions about your project and build accurate expectations about the converting process.

What is Partial Tooling?
If you’ve received a die cut quote, you’ll know that you are responsible for covering “partial tooling,” which is the initial cost of the die cut tool.
Outside of the initial tooling cost there’s retooling and eventually replacing. Each die has a certain number of retools available because of the general construction of dies. As you use those retools, the die will reach its end of life and we’ll have to replace it.
However, you will most likely only pay the partial tooling cost as Strouse covers most re-tooling, maintenance, and other follow-up costs. The main exception is design changes, which are not covered.
INITIAL TOOLING PAYMENT
When you pay the initial cost of tooling, you’re paying for the rough cost of the tool itself and the first re-tooling.
Every die cut tool is custom-made for a project, which is why you pay the initial cost. However, the blade of a die cut tool endures constant stress and dulls over time. As the ones using and maintaining the die cut tool, Strouse decides and subsequently handles necessary re-tooling.
Since you’ve already bought the die, we cover your re-tooling after the initial cost, except if you re-design your part and the die needs replacing.
In the end, you’ll end up paying the initial tooling cost (the price of the die cut tool and first re-tooling), while Strouse will take care of the following expenses.
THE LIFESPAN OF A DIE CUT TOOL
Because die cut tools spend their lives dulling, they eventually need to be re-tooled or replaced. As your converter, Strouse can anticipate and prepare for eventual re-tooling.
There isn’t one way to predict how long a die cut tool will last, but certain factors allow us to predict how often your tool will need replacing. Die cut tools can last for a short or a long time depending on:
- What you’re cutting to
- What you’re cutting through
If your part design has many layers, you could cut all the way or partially through the material. Cutting all the way through, or “zero-clearance” cutting, will make the blade contact the metal anvil, causing it to dull faster. Kiss cutting, or partially cutting through the material, allows your blade to last longer.
Your die cut tool also wears down at a much quicker rate if you’re using highly abrasive materials.
For instance, thermal transfer paper is a highly abrasive material with a tough coating. Because it’s difficult to cut, tooling manufacturers often build specialized tools for it entirely.
Another example of abrasive material is white ink, which contains titanium dioxide. Cutting white ink on a die cut press causes the tool to dull prematurely. In short, abrasive materials cause your die cut tools to wear down quickly, which leads to a higher overall tooling cost and more frequent re-tooling.
RE-TOOLING IS INEVITABLE
Re-tooling occurs when the die cut tool reaches the end of its natural lifespan or you alter a design.
Most changes to your design’s dimensions or tolerances will lead to re-tooling. Die cut tools are highly customized, and any changes to your process, including material changes, might warrant a costly tooling replacement.
With how expensive replacement tooling can be, it’s essential to provide your tolerances accurately. Are your tolerances what you need in your product, or are they the typical “boiler-plate” tolerances you’d send to a machine shop?
If you don’t do your due diligence in confirming your tolerances, you might end up with a part in desperate need of re-tooling or with needlessly expensive tolerances.
If you already know your part design is likely to change, you can minimize the cost of re-tooling by using alternatives:
Tooling Alternatives
Tooling costs are often a necessary evil for die cut production, yet there ARE a few alternatives.
Using non-production-based (a.k.a. flex tooling) or non-rotary tools can give you custom die cut parts without the high expense of standard, rotary die cut tooling.
NON-PRODUCTION-BASED TOOL (FLEX TOOLING)
Using non-production-based tools, or flex tooling, can be useful for lower-volume products and those still in development.
A non-production-based tool is a thin plate mounted to a cylinder full of magnets; and while it doesn’t last as long as a regular die cut tool, it has a lower initial cost.
Flex tooling is often perfect for thin products like labels and prototype parts, which are typically characterized by lower volumes or design changes. The initial cost of flex tooling is significantly lower than standard tooling, sometimes ranging up to 3x or 4x cheaper in value. In fact, many non-production-based tools cost less than $500.
Of course, flex tooling also has many downsides, such as its limitation on thickness (typically only up to 20 mil), a lower lifespan, the limited size of repeats, and less overall project versatility. Flex tooling isn’t ideal for every project, and if you’re looking to elongate the lifespan of a die cut tool, you’ll want to instead focus on investing in high quality steel.
High quality steel dies are more expensive, but they last far longer without needing replacement. If you’re planning on a high volume and long-term project or need highly accurate final part tolerances, then regular, higher quality die cut tools are likely the best fit for you.
NON-ROTARY CUTTING TOOLS
Non-rotary cutting tools, such as laser and digital cutting methods, don’t require the purchase of a die cut tool. Laser and digital cutting rely on the machines, so there is no tooling cost.
Many of our samples and prototypes are made on a laser or digital cutting machine because they don’t require us to order any rotary die cut tools. Yet, due to their limitations, non-rotary cutting tools aren’t ideal for every project or situation.
Non-rotary cutting tools are used for low volume projects, often leading to a higher price per part. Also, many materials cannot be laser cut despite how laser cutting achieves tight tolerances.
Digital cutting machines don’t achieve as tight tolerances as the laser but cut objects of a larger size, so the cutting method you use boils down to your specific product needs and how we can help you achieve them.
How Partial Tooling Costs Can Help You
Die cut tools are expensive, and partial tooling saves you money by ensuring your converter takes care of your eventual re-tooling. You buy the steel and your converter takes care of it.
From tooling maintenance costs to die cut tool replacement, Strouse covers years of fees for each individual project. Assuming you plan to make a decent quantity of parts, you’ll absolutely benefit from the partial tooling system.
If your project is low volume or a one-time production, you may want to try our aforementioned tooling alternatives. Unsure which production method to use? Got any additional questions about manufacturing tooling costs? Schedule a project consultation, or check out our Learning Center for more information.
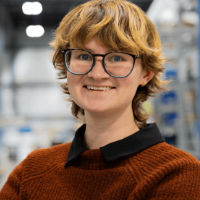