Trying to shield against EMI without the right materials will leave you feeling like you’re wearing a “bulletproof” vest made out of office tape: anxious, unprotected, and way too exposed.
Electromagnetic waves can pass through any material without magnetic properties, including most woods, glass, ceramics, and non-conductive plastics. Therefore, devices that lack proper EMI protection are at the mercy of stray signals.
Over the years, Strouse has helped clients build their designs using different EMI shielding materials. Through discussion, we guide you to choose an option that matches your application goals. Let’s explore what materials you can use for EMI shielding, where to find them, and how to tell which is the right one for you.
What Are the Different EMI Shielding Materials?
EMI shielding materials often consist of one of three metal types in various forms. Sometimes, engineers combine materials to create the best EMI shielding solution.
1. PRE-TIN PLATED STEEL
Pre-tin plated steel costs less than the other conductive EMI metals used in EMI shielding, but it works well for lower frequencies, typically in the kHz range up to the lower GHz range. Carbon steel, in particular, provides low-frequency shielding properties that other metals don’t offer and protects the steel from corrosion and rust.
2. COPPER ALLOY 770 / NICKEL SILVER
Copper alloy 770, also commonly known as alloy 770, consists of copper, nickel, and zinc. Engineers often use it for EMI shielding because it resists corrosion well.
Copper alloy 770 works best as an EMI shield for the mid-kHz range up to GHz. Its permeability is 1, which means it is ideal with MRI machinery where magnets cannot be present.
3. COPPER
Copper is notably different from the copper alloy 770 (a combination of materials).
Of all the metals used in EMI shielding, copper is the most reliable because it works best at reducing both magnetic and electrical waves. Copper can be found in almost any place needing EMI shielding, from hospital equipment to basic home computers.
Copper admittedly costs more than other alloys or pre-tin-plated steel, but it also has a higher conductivity rate, which makes it an effective EMI shield.
4. ALUMINUM
Because of its strength-to-weight ratio and high conductivity, aluminum can be a good EMI shield material. Compared to copper, aluminum has nearly 60 percent of conductivity.
Aluminum's disadvantage is that it corrodes more quickly than other metals and has high oxidation properties (oxidation compromises the metal's integrity and weakens it).
5. EMI SHIELDING FILM AND FOIL
EMI shielding tape, film, and foil each have their place in the EMI shield marketplace.
Although EMI materials can take many shapes, the material and form of the EMI protection depend solely on the type of electronics that need the shielding and the frequencies involved. For instance, conductive silicones serve as window films in commercial settings, shielding electronics from magnetic and electrical waves.
In other instances, technicians use metallic foil or plaited braid to shield equipment wires, or coaxial cables with EMI shields built into the wire construction. Technicians wrap wire bundles in foil or apply cable braid over the entire construction. Even the connectors have EMI shielding with braiding or foil attached to the metal covers, giving the appliance or device complete protection.
Printed circuit board shielding has a ground plane built into it and a metal box covering the sensitive elements. Technicians then surround the delicate components with a Faraday cage arrangement.
Audio speakers have an inner metallic casing that blocks EMI caused by common nearby elements like microwaves or televisions.
When magnetic fields are less than 100 kHz, you can use conductive points and magnetic materials. Technicians will also use sheet metal, metal foam, conductive plastics, or mesh metal screening.
5a. SHIELDING TAPE
Shielding foil tapes have specific characteristics that make them ideal for EMI shielding. They resist corrosion and are flame-retardant. They're also flat and embossed, making them suitable for shaping around odd corners and shapes.
You can find shielding tapes in several places:
- Ground panels for electronic cables and connectors
- Keyboard devices
- Around individual electronic components and cables
- In the seams and holes in shielded rooms.
- Electro-medical devices
- Doors and panels of electronic cabinets
- Around outside of coils, relays, and other electrical components that could attract broadband EMI emissions
- Used around the outside of coils, relays, and other components to prevent broadband EMI emissions
6. EMI SHIELDING FOAM
EMI shielding also comes in the form of carbon foam. Although it has no metallic components, the foam will shield anywhere from 100 Mhz to 20 GHz. Foam has a distinct advantage as an EMI shielding material because it can serve more than one function.
For example, some foam provides fire protection. It also lasts longer in harsh environments than metal would, weighs less than metal, and does not corrode while staying environmentally friendly.
7. EMI SHIELDING SILICONE
Silicone typically cannot conduct electricity. However, if you embed metal in silicone, you create a conductive material that can work well as an EMI shield. Current EMI shield silicone has nickel-graphite, effectively shielding radio frequencies between 20 and 10,000 Hz.
Silicone is flexible, meaning that manufacturers can die cut it to fit wherever EMI shielding is needed. The automotive, aerospace, satellite communication, and electronic industries have all used silicone in their products, often as EMI gasket material.
Many people prefer to use silicone because it resists sunlight and water while tolerating a wide range of temperatures. This is why silicone is used in extreme heat and cold environments, like aerospace engineering.
Where Can I Find EMI Shielding Materials?
If you called us up to ask this, we’d probably reply, “Well, what are you trying to make?”
To find material roll samples, you can always reach out to a vendor (such as 3M or Mactac) about the material you want, although they may not have it depending on the type. However, if you need material or custom-cut samples for a particular project in development, it's probably better to talk to a converter.
While it’s great to understand your requirements on paper, certain materials may behave in a challenging manner that makes them more difficult to manufacture. For this reason, we would recommend reaching out to a converter first to ensure that the material selection is optimized for manufacturability.
Which EMI Shielding Material is Right For My Project?
Choosing the right material depends on a multitude of factors, including the application (type of electronics that need the shielding), relevant frequencies, adhesive requirements, and design tolerances.
If you’re interested in finding the right shielding material, consider reaching out to test your design.
At Strouse, we’ve found that a thorough design evaluation leads to more accurate prototypes for testing your EMI RFI shielding materials. For an accurate sample you can trust, reach out to begin the discussion about your part design.
If you don’t have a technical drawing yet but would be interested in a sample, figure out what you need in a drawing before contacting us.
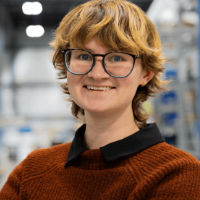