Like millions of other people, you may own a medical device to monitor your health. Yet, you might not know what diagnostic medical devices look like or how they're made.
Microfluidic devices read fluid samples to provide crucial information to patients and their caregivers. They must have specialized materials to ensure accuracy as these critical tools are designed, manufactured, and assembled.
Because they are usually small and have intricate channels and circuits, microfluidic devices require specific material properties. Over the past three decades, Strouse has worked on many complex microfluidic applications.
In previous articles, we covered the four key materials for building microfluidic devices and how microfluidic fabrication technology allows for many diagnostic applications. Today, we’ll explore converting adhesive materials and provide insight into fabrication strategies when developing advanced microfluidic devices.
Types of Microfluidic Device Tape
Converted (cut and processed) adhesive tape is the foundation of many microfluidic devices. The type of tape used often depends on its function and/or appearance.
1. SINGLE-COATED TAPES
Single-coated tapes are adhesives anchored to a substrate and can be used with or without a secondary liner. If there is no liner, the substrate’s backside has a surface treatment or coating that allows the adhesive to release when unwinding. They're typically strong and conformable; some can adhere to another component (tape stacking).
2. DOUBLE-COATED TAPES
Double-coated Tapes are a single substrate with adhesives on both sides, which could be different adhesives depending on the adhesion levels needed. These can be constructed with two single-coated or one double-coated liner that releases both adhesive layers.
3. TRANSFER ADHESIVES
Similar to double-coated tapes, just without a substrate, transfer adhesives are made with either a two-sided release-coated liner or two single-sided liners. The differential in the release of the liners needs to be correct because the liner might pick or split during processing if the two release coatings have similar adhesion.
Microfluidic Device Tape Components
It’s also essential to understand how each component of tape functions when creating microfluidic devices. These part components allow microfluidic devices to protect samples, transport fluids, and help with accurate detection.
ADHESIVES
This one sounds simple: adhesives bond tape to a surface. In microfluidic devices, tapes bond to plates to seal sample-well boundaries or to components to build the device (labs-on-a-chip, test strips). Due to temperature changes during processing, adhesives must be chemically stable.
CARRIER (OR BACKING)
The carrier (or backing) is a component that dictates a tape’s mechanical characteristics and needs to be selected based on:
- How that tape should perform (does it need to be rigid, stretchy, permanent, or temporary?)
- How it will be applied (will it be hand-applied or automatically dispensed?)
- How it will be processed (will it be slit or die-cut?)
Some microfluidic tapes have surface modifications added, enabling hydrophilic characteristics, creating better adhesion, or helping with adhesive release.
LINERS
Typically a coated paper or film, liners are clean surfaces that cover the adhesive and protect it from exposure and damage. Some liners help with processing only, and some stay with the tape until it’s used. Liners are available in numerous substrates based on the user's needs.
Converting in Microfluidics
Expertise in converting for medical and healthcare manufacturing ensures that your microfluidic devices deliver consistent and reliable performance, lot after lot.
3M MICROFLUIDIC TAPES
If you’re looking for popular 3M Microfluidic Tapes, here are a few examples:
- 3M 9793R Diagnostic Microfluidic Medical Tape
- 3M 9795R Advanced Polyolefin Diagnostic Microfluidic Medical Tape
- 3M 9792R Aluminum Diagnostic Microfluidic Medical Tape
- 3M 9964 Clear Polyester Diagnostic Microfluidic Medical Tape
- 3M 9965 White Polyester Double Sided Diagnostic Microfluidic Medical Tape
- 3M 9960 Diagnostic Microfluidic Hydrophilic Film
- 3M 9962 Diagnostic Microfluidic Hydrophilic Film
- 3M 9984 Diagnostic Microfluidic Surfactant Free Fluid Transport Film
- 3M 9969 Diagnostic Microfluidic Adhesive Transfer Medical Tape
CONVERTING MICROFLUIDIC APPLICATIONS
A full-service adhesive tape converter should work with advanced materials for microfluidic devices, including:
- Bioassay compatible tapes for use in PCR, qPCR, and ELISA, designed to minimize the potential for chemical and optical interference
- Hydrophilic films for fluid transport, including specialty coatings and materials that enable efficient flow of fluids through capillary microfluidic channels
- Films and specialty materials for solutions such as membranes, polyester films, coatings, engineered fluids, etc.
- Spacer tapes with low build-up of residue to ensure the thickness of the material meets the specifications and requirements of your device to ensure capability with your chemistry
- Porous membranes used for filtration
- Electronic assembly tapes
- Connectors
Using trusted materials in your products’ construction is essential, but working with a trusted converting partner is equally vital. So, let’s ask: What abilities can a specialty converter provide?
- ISO 7-Certified Cleanroom: We ensure the quality of the materials and converted products
- Quality Management System registered to ISO 9001 and ISO-13485: We insist on the highest level of consistency; only the best processes and procedures deliver tight-tolerance adhesive solutions required for medical devices and the FDA
- 3M Preferred Converter of 3M Medical Materials and Technologies: We leverage our partnership with the global leader in adhesives to get samples of materials in the dimensions and format you need for testing
Ask a Strouse engineer about adhesive solutions for your design. We’ll help you deliver accurate and easy-to-use application components, including layered materials for biosensors, integrated consumables for lab-on-a-chip applications, diagnostic consumables, devices incorporating microfluidics, and more.
To learn more about microfluidic device fabrication in converting, check out the resources in our Learning Center.
Originally published: February 17, 2021
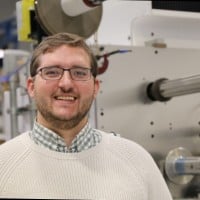