A converted product’s carrier or backing material is one of the most important decisions when designing pressure sensitive adhesives. The carrier has to possess the right qualities to match the application (will it be hand applied or automatically dispensed?) and the processing (will it be slit or die-cut?).
Recently, we explored the basics of release liners in this article. In today’s blog post, we’ll dive into the physical components of backing (or “carrier;” we’ll use both terms throughout) and how it helps the converting process.
What Does Carrier Material Do?
The carrier is the thin, flexible material onto which the adhesive is applied, and it helps form the structure of the material, transports the adhesive, holds the material together, and protects the adhesive. The thickness of the carrier can be crucial for converting and die cutting the adhesive. For instance, a thicker, stiffer backing helps the product maintain its shape and stability.
Here’s the construction of a double-coated adhesive:
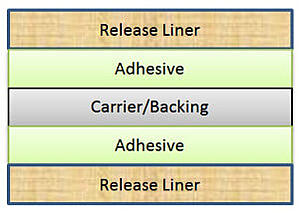
The carrier is the middle piece that holds, or “carries,” the adhesive on both sides, which becomes exposed when the release liner is removed either by hand or using automation.
What is Carrier Material Made Of?
There are several options for carriers. Adhesive can come on polycarbonate, polyester, PVC, and other carriers. Yet, as mentioned earlier, it really depends on the application used and the process involved.
Here’s one example of that. 3M produces a conductive polycarbonate carrier especially for electronics applications. This carrier has electrical properties that help protect static-sensitive components with electrostatic shielding and electrostatic decay.
What Happens When You Need Two Different Types of Adhesives on Each Side?
When you have two different substrates on each side, there is a possibility that you’ll need to have two different types of adhesives on each side of the carrier. This product may come standard and it may not; it depends on your particular application and your needs. If it doesn’t come standard, a high-end converter can source the correct adhesives and implant the correct carrier to build the double-coated stackup on press using qualities from the ideal materials.
Why is Adhesive Backing Crucial to Converting?
In the 3M example above, the right backing matches how it’s used. That’s a specialized carrier developed for a specific purpose.
Let’s look at backing from the point of view of a converter that takes raw materials (usually in large rolls) and makes them into usable parts. They don't make the adhesive or the film or the plastic. The converter does, however, know these materials inside and out, and they know virtually every company that makes the materials.
That means a converter is informed and positioned to properly source the exact right materials for a product. The converter knows how to take the materials they select and turn them into products that customers want.
You can see why selecting a full service adhesive tape converter that knows all the benefits of different carriers is a smart move. If you need any help with selecting an adhesive backing for your product, give Strouse a call today (800)-410-8273 or you can ask an engineer about adhesive solutions today!
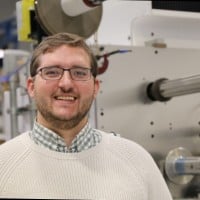