You’re reviewing your updated design files when a vital question arises: will this product update affect your manufacturing process?
The answer? It depends on the changes you’ve made.
Product updates are a common occurrence, but unfortunately, they may cause you to reshape your manufacturing process. Having received product updates for hundreds of projects over the years at Strouse, we want you to be prepared.
First, we’ll review the potential changes you might make to your products. Afterward, you should be able to predict which updates will likely lead to production changes and what those changes will entail.
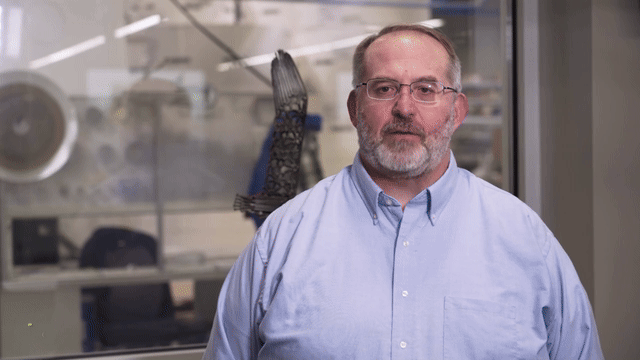
How are You Changing Your Product?
Product updates typically come in three forms: a change in material, part geometry, or packaging.
The type of change you make will impact the level of adjustments Strouse has to make to your production later on and the level of additional costs incurred as a result.
CHANGE IN MATERIAL
Product updates that involve changes in the material could either lead to significant cost and production changes or no changes whatsoever.
For instance, if you were using a double sided tape and decided to switch to a slightly thicker but very similar double sided tape, you might not encounter any issues.
However, if you switched from double sided tape to transfer tape, there would be a much more significant magnitude of change. In this case, the two materials could require different methods of handling and processing, which might cause more significant changes at a higher level.
It’s worth noting that ANY material changes can have a domino effect on other parts of the process. Changing your material from a 2 mil thickness to a 5 mil thickness may require you to purchase new die cut tooling. It also could result in a bigger roll of material that requires a larger box, ultimately resulting in a slightly higher shipping cost and more consumed storage space.
PART GEOMETRY
Changes in part geometry range from minute to significant, so how will you know whether it affects your process?
These changes typically won’t result in process or tooling changes:
- Updating non-critical tolerances
- Loosening tolerances
- Changing materials that are the same thickness and have the same liner thickness
On the other hand, these examples might result in process or tooling changes:
- Changing the radius on a corner
- Changing the position of an internal cut
- Tightening tolerances
- Changing materials that are very different in thickness
Changing the shape of your die cut part will always run the risk of re-tooling. Die cut tools are customized, and changes in the measurements or the design tolerances will result in adjustments or new tooling entirely.
When you’re changing both your material AND your part geometry, the part will essentially need to re-enter part development while we figure out whether the current process is still applicable. With multiple significant changes, it could be necessary to plan out the step-by-step process once again and test it on a trial.
It’s challenging to draw the line between what counts as a critical tolerance versus a non-critical tolerance. If you have any questions about a specific design, don’t hesitate to get in touch with us about changes you plan to make.
NEW PACKAGING
Packaging is often built into production, and changing its format can be a larger hassle than many customers realize.
Modifying the measurements or quantity of your product’s packaging can result in a more complex process depending on the current setup and your request. It might lead to a slight delay or cost increase if the change is significant.
What Does a Product Update Cost?
Product updates can result in many additional costs, including new tooling, additional labor, product delays, and more.
Die cut tools are customized for each part they cut, and new tooling means paying for new die cut tools entirely. There are no cost advantages to editing existing tooling to match the new design. Tooling can be expensive, so you’ll want to discuss the impending tolerance or measurement changes with your converter to see if any design adjustments could help reduce the strain of a considerable expense.
As previously mentioned, changes in the material or part geometry can also necessitate further testing to ensure the process works before purchasing a large quantity of material.
Unfortunately, trials entail both material and machine run time, which comes at a price. Product updates aren’t always cheap, but luckily there are ways to prepare and mitigate some of its costs.
How Can I Prepare for My Product Update?
Preparing for a product update is often a multi-step process, but you can be proactive by getting your converter involved early on.
From our experience, product updates often forget to account for manufacturability, which can lead to a far more complex and expensive part.
Waiting on outside factors such as FDA approval can be a lengthy process requiring input and leaving you with a different part from when you began. Certain changes can even make your design nearly impossible to mass manufacture, which you’d surely want to know sooner rather than later in the process.
The best way to avoid designing an unnecessarily complicated product is by keeping your converter up to date on the changes you’re considering.
Looking for more info on product updates? See additional factors to consider before changing your design above, or see more information in our Learning Center.
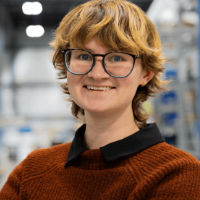