Remember skinning your knee when you were a kid? As inexplicable as it was that you didn’t pull off that amazing move on your bicycle that you’d been practicing all day, it was nice to have something available to help you heal. If a standard bandage wasn’t up to the task, you may have relied on some gauze and wound dressing tape to do the trick.
In addition to being found in homes, medical professionals also count on it for much more severe concerns in doctors’ offices and hospitals worldwide. With wound dressings, you have the adhesive, backing, and gauze (if needed) that must all work together to protect and assist with the healing of injuries, surgical incisions, and more.
What needs to be considered during the manufacturing process? It’s so unlike many other adhesives due to its critical life-saving uses and routine patient care, that you need to take a different approach. Let’s delve into some of the vital aspects of manufacturing wound dressing tape unique to this adhesive.
What Considerations Go Into Creating Wound Dressing Tape?
Flexibility
Wound dressing tape is meant for unpredictable surfaces with a lot of movement, so it needs enhanced flexibility compared to many other adhesives.
If it’s on someone’s elbow, it needs to be effective whether the elbow is bent or outstretched. Or maybe it is tasked with holding gauze on a person’s face. In that case, it has to withstand the constant changes in facial expressions. If you’re going to laugh, the wound dressing tape needs to laugh with you!
Adhesive Strength
Related to flexibility, the adhesive itself must be strong enough to stick to a person’s skin or gauze for as long as needed while handling those different movements and other factors.
Then, when it’s time to remove the adhesive, it has to peel off as pain-free as possible. A manufacturer must consider the adhesive chemistry and specifics when developing wound dressing tape. The wrong adhesive may not only be ineffective, but it could even make things worse.
Waterproofing
Waterproofing isn’t just about keeping water out — it’s also about keeping moisture in. Wound dressing adhesive should keep in and keep out precisely what it needs to.
If a water-based balm or antibacterial liquid is used on the wound, for example, it must be contained firmly inside the wound dressing as needed. By the same token, everyday hand washing and the like shouldn’t interfere with the wound dressing and its healing process.
Testing
How do you ensure the wound dressing tape is flexible enough and remain stuck without doing more harm? Testing.
Testing wound dressing tape can include determining its elongation, adhesive strength, waterproofing, and more.
It’s crucial to know the wound dressing tape will work as it should before going to assembly. Developing some different styles and producing samples of them to try out before committing to an entire assembly can save you time and money.
Cleanliness and Sterilization
Sterilization is one of the most significant differences between wound dressing tape and other adhesives. This tape will not be stuck to a wall or used to create a seal between two inanimate objects. It’s essential that this tape is sterilized to avoid infecting wounds.
Typically, sterilization comes after the manufacturing and conversion processes, at the end and shortly before final packaging. But as the first step in its sterilization, the manufacturing and converting must be done in a cleanroom setting. This is a separate room from where other adhesives are made or converted.
Strouse, for example, maintains a clean room and appropriate protocols where we convert the wound dressing tape separately from other adhesive products.
That environment must be free of biological cells or other potential contaminants. While that’s aimed for in any manufacturing process, it is critical for adhesives that will directly contact with a person’s body, especially when it’s an open wound. The room must be certified, and it’s vital to keep up the cleanroom process consistently.
That’s key: consistency. Sterilization comes afterward, so a consistently clean process must be adhered to before that even happens so the sterilization can be done efficiently.
The sterilizer will thus know exactly what went on before the material is sent to them. They can set up the sterilization process accordingly rather than having to make adjustments for each product.
FDA Approval
Everything comes down to FDA (Food and Drug Administration) approval. Wound dressing tape is a medical item subject to intense regulations. If it doesn’t meet FDA standards, it’s not at the supermarket or your local hospital.
Everything we mentioned before must be factored in from the get-go. A wound dressing tape producer must know what the FDA requires and develop it with all these considerations.
Learn More: 4 Critical Considerations When Choosing a Wound Dressing Tape
Converting with Strouse
Once wound dressing tape is developed and needs to be cut to the correct size, it’s time to get a converter involved. That’s where we come in!
Strouse is a Medical 3M™ Preferred Converter, which means we’re trusted partners of an industry leader in a multitude of adhesive products, including wound dressing tape.
There’s a validation process with the FDA and its requirements, and if manufacturers can have their wound dressing adhesives pre-validated, that can cut as many as six months off the cycle time. That’s what a 3M and Strouse partnership brings to the table.
Strouse works efficiently with a process called 1-Pass Production — taking roll goods to heat-sealed products in a single pass. This is meant to increase conversion speeds and improve accuracy and quality, among other benefits, without cutting corners. Would you like to learn how we can make this work for your project? Give us a call or click the link below today!
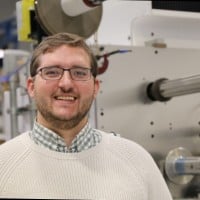