Would you slap painter’s tape tape under the hood of your car? If anything, it would probably just create a fire hazard. While some adhesives can’t take the heat, many tapes are specially designed to withstand high temperatures.
As a company that often works closely with aerospace, automotive, and electrical industries, Strouse has helped build hundreds of different heat-resistant components.
Temperature regulation issues can have disastrous consequences for machinery, which is why today, we're discussing heat-resistant tapes in greater detail—explaining how they work, why they fail, and offering a multitude of material options.
What Classifies a Tape as Heat Resistant?
As you may have already guessed, “heat resistant” is a relative term. Most durable tapes can withstand operating temperatures of up to 250-300°F, but once you get up to 400°F or higher, you need to start looking at specific materials for high-temperature applications.
How To Choose a Heat Resistant Tape
Choosing the right heat-resistant tape means picking out a product that will meet your specific heat rating. Tapes are only as strong as their weakest link. In this context, it means we need to check the heat rating of all the individual components.
A tape consists of a few primary components: the adhesive(s) and the carrier/backing(s). When any of the components (adhesives, carrier, or backing) fail, the tape is compromised. For example, a foil backing that can withstand 600°F can fail at 300°F if the chosen adhesive is only good up to 300°F.
Another factor to keep in mind is short-term (minutes or hours) versus long-term (days or weeks) temperature resistance. The short-term vs. long-term heat resistance listed on a particular product can be as far as 100°F apart. Mistakenly using a tape with short-term resistance could work temporarily and then fail over time.
7 Types of Tape that Can Resist Heat
If you’re searching for high-temperature materials, your first thought is likely, “Which of these heat-resistant tapes will work best for my project?”
Having worked with a range of materials, we’ve determined that these adhesives are some of the most popular materials for heat-resistant bonding and gasketing. The following list will break down these different types of tape so you can make the best choice during your material selection process.
1. SILICONE ADHESIVE TAPES
Silicone is considered almost exclusively when you talk about heat-resistant tapes. Silicone adhesives are often used in high-temperature aerospace, automotive, construction, and electrical applications; plus, silicone rubber is used for many high-temperature gaskets.
The bonds of silicone adhesives can typically withstand -60°F to 500°F (-51°C to 260°C), at least for short-term uses. Many tapes can survive short bursts of high heat without long-term applications, so you’ll want to keep an eye out for this when perusing different technical datasheets.
2. KAPTON (POLYIMIDE) TAPE
Kapton tape, also known as polyimide tape, is often used in aerospace applications due to its extreme heat resistance and insulating properties.
Kapton can withstand temperatures ranging from -103°F to 500°F (-75°C to 260°C), but supposedly it has functioned in temperatures as low as -320°F to 752°F (-196°C to 400°C).
3. FOIL ADHESIVE TAPES
Foil adhesive tapes (aluminum, copper, stainless steel, etc.) are used for EMI and RFI shielding, HVAC sealing and insulation, and packaging.
The temperature performance range of a foil tends to be around -65°F to 600°F (-54°C to 316°C), although the temperature resistance will likely depend on the type of foil you’re using.
4. GLASS CLOTH TAPES
Glass cloth or fiberglass cloth tapes are used for sound insulation, material reinforcement, and more. Similar to Kapton and foils, glass cloth is extremely high-temperature resistant and can handle elevated temperatures of over 500°F (260°C).
5. POLYESTER (PET) FILM TAPE
Polyester (PET) tape is used for electronic joining, high-temperature masking for powder coating applications, and splicing. Polyester tapes can often last in environments from -94°F to 400°F (-70°C to 204°C) and even higher temperatures with shorter bake cycles.
6. ACRYLIC ADHESIVE TAPES
Acrylic adhesive tape is used for powerful bonding applications in automotive, medical, and many other industries. They are high-strength and flexible components used to replace mechanical fasteners like screws or rivets.
Although acrylic tape can be heat-resistant, and reach 400°F (204°C), most of it falls well below that limit. Depending on the tape, it’s generally agreed that the lower limit is -20°F to -40°F (-28°C to -40°C).
Finding the Right Heat Resistant Tape
Choosing the right tape depends on your unique product, but there are a few simple steps you can take to ensure you find a tape that meets your specifications.
1. Reach out to a flexible material converter and share your application and your unique design requirements.The converter will be able to approach your project from a holistic perspective, including manufacturability.
2. Contact your tape supplier, such as 3M, tesa, Avery Dennison, Mactac, Berry, etc., and share your application and unique design requirements.The supplier will be able to make suggestions based on the application or your design requirements, but not as much from the manufacturing perspective
3. Online research: Many product technical data sheets are searchable and available online with information on temperature resistance.Whether you contact a supplier or do online research, you’ll still need to address manufacturing. This might lead you to a material converter like Strouse, who will oversee critical manufacturing, cost, and feasibility factors.
If you’re building a heat-resistant product, you’ll want to perform tests to prove your material and design can withstand the heat once they’re put to the test. Consider requesting a sample or reading more about the prototyping process in our Learning Center.
Originally published: August 15, 2023
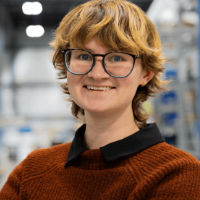